Metallurgy automation
Autocontrol system for continuous casting process Continuous casting process is to make the molten steel cast into billets. It is difficult to assure the high output and good quality just by manual control, especially for high speed continuous casting machine. The benefits of continuous casting automation includes: to increase yield rate by more than 1.5%, improve the billet quality, increase the utilization rate of the continuous casting machine to more than 98%, save power by more than 10%, improve the usability and life of the continuous casting machine, and make the maintenance cost reduced by 1/3. Continuous casting autocontrol system includes two levels of control: the basic automation and the process automation.
Autocontrol system for refining process outside the furnace Refining process outside furnace is the smelting process outside the first smelting furnace (such as converter, electric furnace). It is used for regulating temperature, desaeration, wiping off inclusions and impurities, regulating components, so as to realize the following goals: ¢Ù Accurately controlling molten steel components. ¢Ú Temperature and components of molten steel meet the requirements of continuous casting process and good interior and surface quality of the billets. ¢Û Desaeration of the molten steel (H2, O2 ,N2). ¢Ü Wiping off most of the sulfur and phosphor from the molten steel. ¢Ý Decarbonization of the molten steel up to the specified value. ¢Þ Wiping off the impurities of the molten steel.
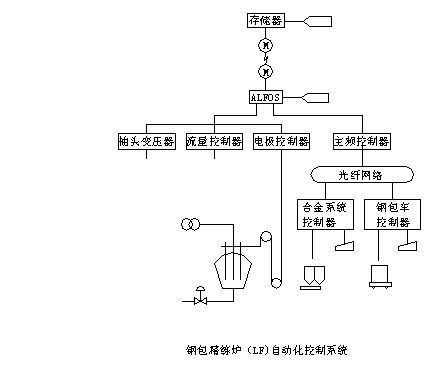
Autocontrol system for converter steel-making Converter steel-making has become the most widely applied steel-making method in the world. The proportion of converter steel-making reaches above 90%. It breaks the conventional mode of converter steel-making, changing the process from single converter smelting to the new technology of molten iron pretreatment, converter smelting with blasting oxygen and argon, refining outside converter and continual casting. In the new process, oxygen converter becomes the new technical tache from the original dominant position. Its object is mostly aiming at molten steel decarbonization and heating-up. Converter autocontrol system can increase output, assure the molten steel quality, reduce the power cost, improve the operation and make the furnace service time longer. It has prominent economy benefits, and also can make the temperature deviation reduced by 40%, carbon deviation reduced by 45%, after-blow rate reduced by 60%, and output increased by 10%. Therefore the investment of automation can be taken back within 12 months.
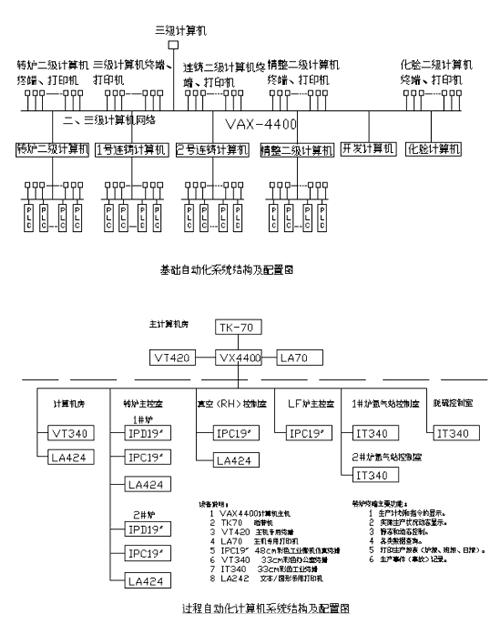
Autocontrol system for blast furnace Our company has been engaged in research and developmental for the blast furnace autocontrol system for a long time. Autocontrol system for blast furnace includes three levels of control: equipment control, process control, and factory management. Equipment control: autocontrol system for the charge and make-up of the materials, the furnace roof without hopper, and the hot air furnace equipment. Process control: model calculation, process data processing, equipment diagnosis, management database of furnace campaign life, production report forms and technological parameter management and so on. Factory management: production management for the iron works, realizing the communications by computers among raw material workshop, coking workshop, sintering workshop. The local computer is in charge of production coordination in the iron works, and communications with company management computer.
Autocontrol system for gas tank For gas tank, the autocontrol system includes two parts: the coal gas recovery autocontrol system and the coal gas detection meters. Autocontrol system is to reclaim coal gas in a safe and dependable manner by means of various on-site detection meters and the control model for gas recovery.
Steel rolling automation The complete automatic packages are applicable to high-speed wire steel rolling, strip steel rolling, and medium plate steel rolling.
Low voltage control panel (cabinet) XL-21 power cabinet PXT series distribution cabinet GGD AC low voltage electric cabinet GCK low voltage on-off distribution cabinet XJ series autotransformer distribution cabinet PGL, GGK, MNS distribution panel Non-standard distribution cabinets, PLC cabinet, and frequency conversion cabinet Electrical and electronic AC devices: KGY series electrophoretic painting power source controlled by microcomputer KGS21 rectifier for electroplating KGC rectifier for charge or discharge KTR AC soft start series KT computer-controlled power regulating cabinet Simulation display: Simulation display for various kinds of production lines, computers network configuration monitoring, and autocontrol system for various processes. |